Member Profile: Wiktor Kidziak
10 April 2015
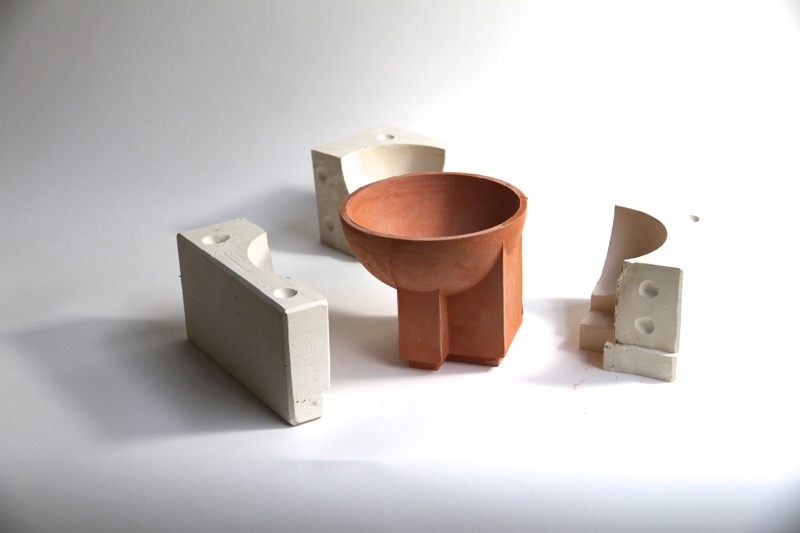
This is the first in a series of brief interviews with our members, to draw out what they've been doing in the makespace.
Wiktor Kidziak
MArch Architecture (ARB/RIBA Part 2) The Bartlett School of Architecture
Wiktor has recently started making ceramics – slipcasting liquid terracotta clay into plaster moulds. With this technique he is able to make hollow objects - lightweight interlocking model assemblies of facades, from an architectural point of view.
He finds the ceramic body is interesting; it has different properties at different temperatures. It works as a cooling façade, sucks moisture at night and retains it, evaporating and cooling through the day. Our technicians explained that this can be controlled by firing temperatures, when the terracotta clay is fired at a higher temperature it becomes darker red, stronger in compression and more efficient. Some parts of Wiktor’s final model are columns, some facades, and you can tell the structural strength from the shades and gradations of the clay. The technicians advised on the properties of glaze to seal the surface and to give different environmental and structural properties. Wiktor says that some student architects show structural properties in their models through colour, using 3d print, but by using differently fired ceramic it seems more holistic.
Wiktor likes that by just being in the makespace you find out things about materials. He was inspired to try using material hybrids by watching other members pouring pewter – which got his mind working, and he has started experimenting with using metals in porous materials, investigating the possibility of integrated electrical systems in architectural components.
He attended the animatronics masterclass workshop – at first just for fun but realizes that all these experiences influence your ideas and has started thinking about moving parts in his work.
As his Masters project focuses on a ceramics cooperative factory in India, he first learned how to use the potters wheel, and likes the interface between traditional and newer forms of making – it can be a freer way of creating forms with rotational symmetry than 3d printing - the go-to architectural modelmaking method these days. He learned a lot about working with plaster, which looks simple but finds it actually very technical when you are using it for ceramic moulds. What he’s learnt about mouldmaking has allowed him to mix techniques, like CNC milling the negative of the form directly into the mould.
He says:
"Material understanding is super important in architecture. In this age of beautiful digital renders, we need materiality, it’s the future – that’s where innovation happens, and will make buildings more environmentally appropriate."
He’d like to look more at metals in the future, welding and combining liquid metal and ceramic hybrids. He’s also interested in glass and what happens in the kiln.
He finds the tools in the makespace exceptional, but what really makes it special is our technical staff Rich and Zac:
"the freedom they give you and the comparitively stress free environment here. They are really willing to spend time with you and look at other stuff, other ideas and techniques. They have the time to engage with you more. It’s a true learning space."
In future he thinks it might be a good idea to get some sort of member mentorship programme going, hooking people with skills up with learners - members giving a class about what they’ve been making, which would be useful to both parties - there’s lots of expertise at UCL. He wants to meet other people through making.
To see more member projects, follow our members project page: instituteofmaking.tumblr.com